Buildability is a little known consideration for most young architectural designers who are just starting out.
Unlike sustainability, who is the much louder cause from many senior architects - buildable design is easily achievable and is easy to understand.
In this post, I will share how buildable design is done, key definitions and design considerations.
Note : This posts serves as a guideline. It is based on building regulations from Singapore, so please consult your country’s building codes as well.
In this post:
Aspects of Buildability
Design Considerations
How to Calculate Buildable Score
Pro Tips
Aspects of Buildability
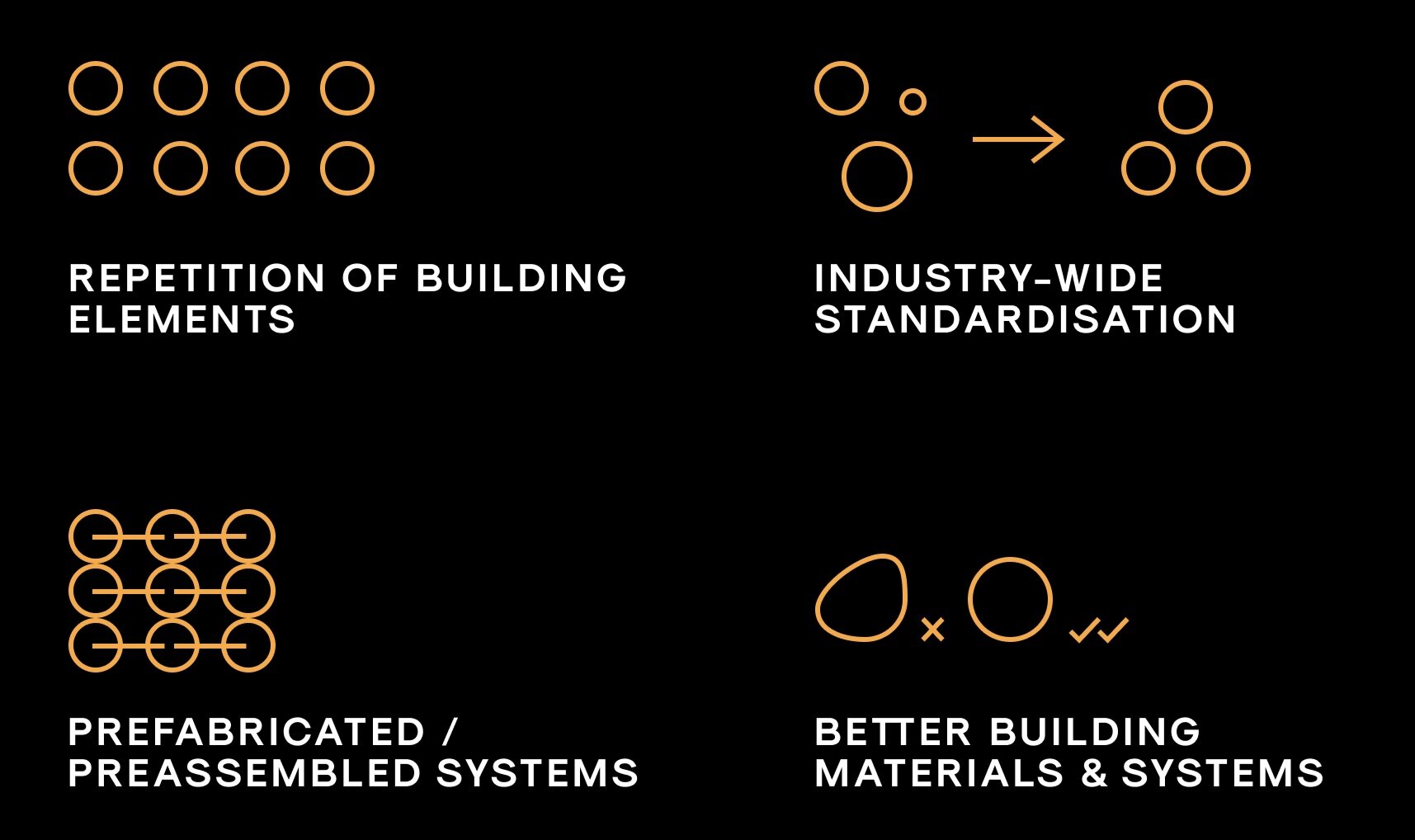
The above diagram shows the four main aspects of buildable design and they are explained below:
Repetition of Building Elements
Position, size and type of structural elements (columns, beams)
Gridlines across different levels
Industry-wide standardisation
Structural wall openings for door and windows
Floor-to-floor height
Staircase tread and riser dimensions
Pre-fabricated/pre-assembled systems
Precast staircases
Pre-assembled steel staircases
Prefabricated Bathroom Units
Better building materials & systems
Drywall
Precast Concrete Systems (wall, columns, beams)
Roof systems (Integrated metal roof on steel truss)
Floor casting (welded mesh should exceed 65%)
Design considerations
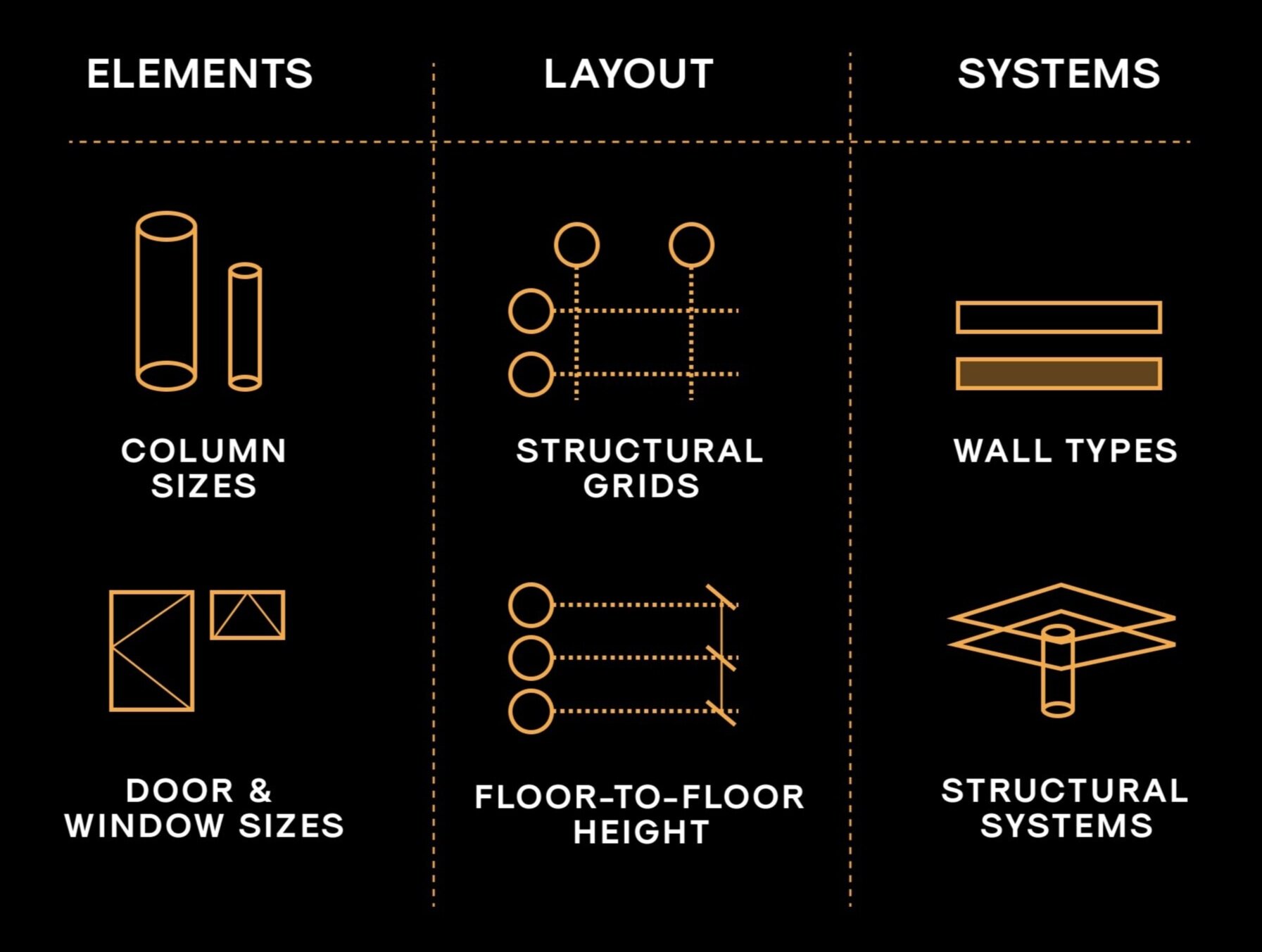
In this section, we will learn more about the various design considerations architects should bear in mind while considering buildability in their design.
1) Standardisation of Building Layout
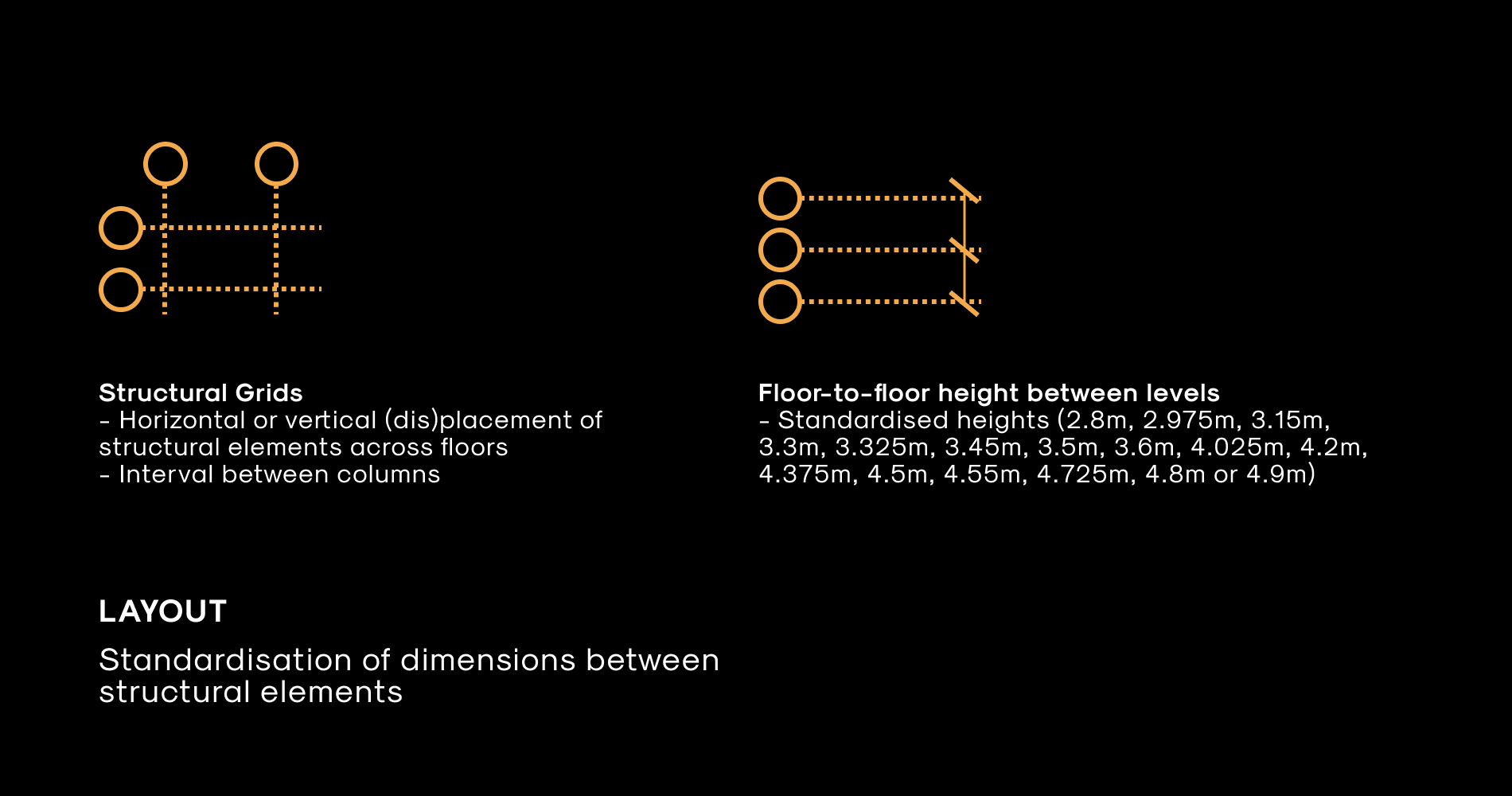
At the prelim design stage, architects should work with engineers to establish the structural grid and floor-to-floor height before anything else.
This is because this will implicate the extent of buildability of the design.
By using industry standard dimensions, you can be sure of the ease of construction as there will be straightforward systems that be used for building elements.
Want to learn more architecture and get a headstart?
Get your copy of the exclusive PDF download - 400 pages, 20 topics, crisp diagrams and searchable text!
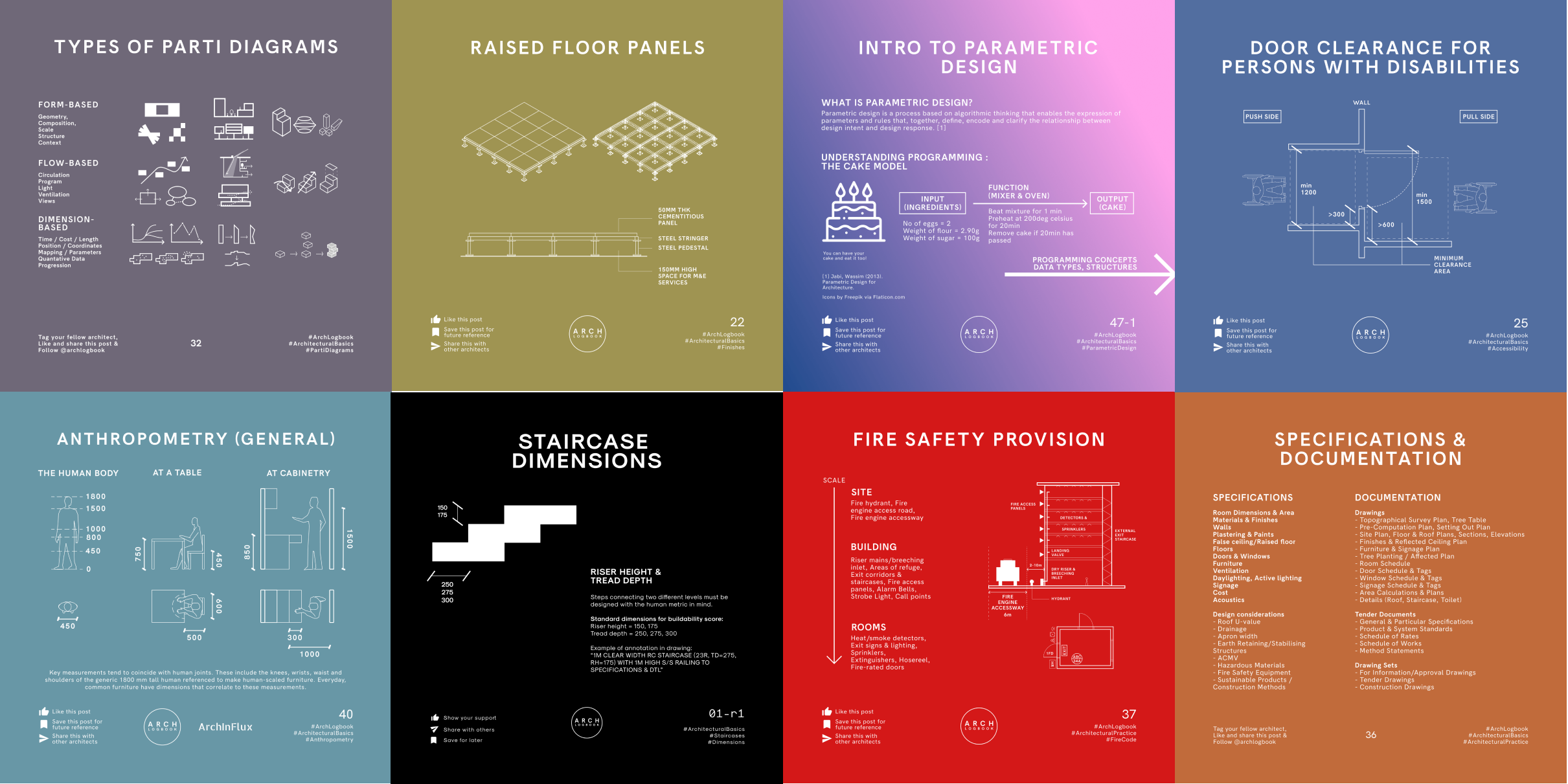
2) Standardisation of Building Elements
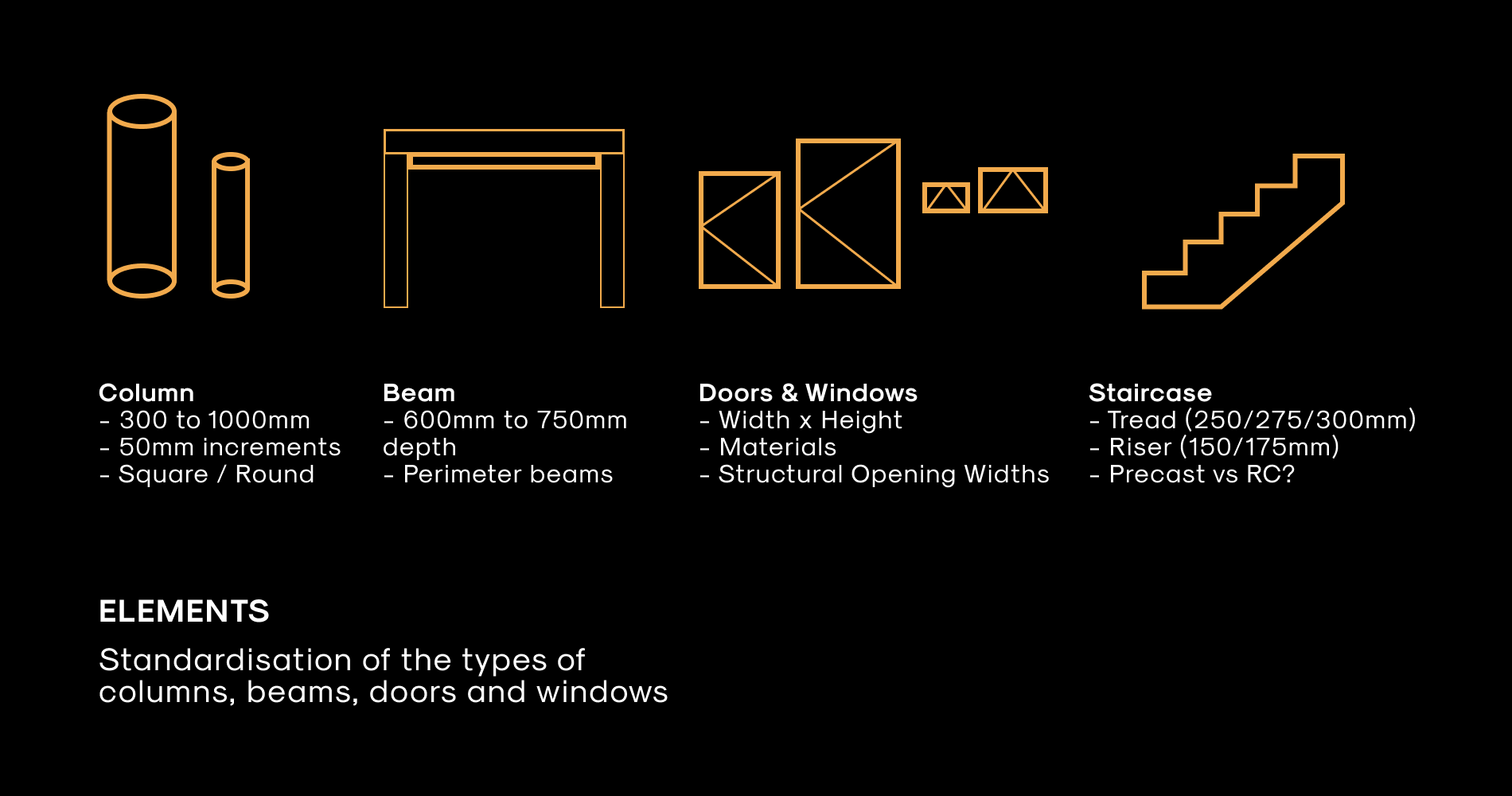
Once the floor-to-floor height and structural grid is finalised, we should consider the range of building elements.
At the detailed design stage, architects and engineers need to work together to optimise the number of types of building elements.
For buildability score calculations in Singapore, more points will be awarded by the decreased number of types of these elements. A good guideline will be 3 types per element - for example, have only 3 column sizes for the whole building.
Another example will be using industry standard door structural openings:
- 900mm, 1000mm, 1100mm, 1200mm, 1250mm, 1500mm, 2000mm
3) Standardisation of Building Systems
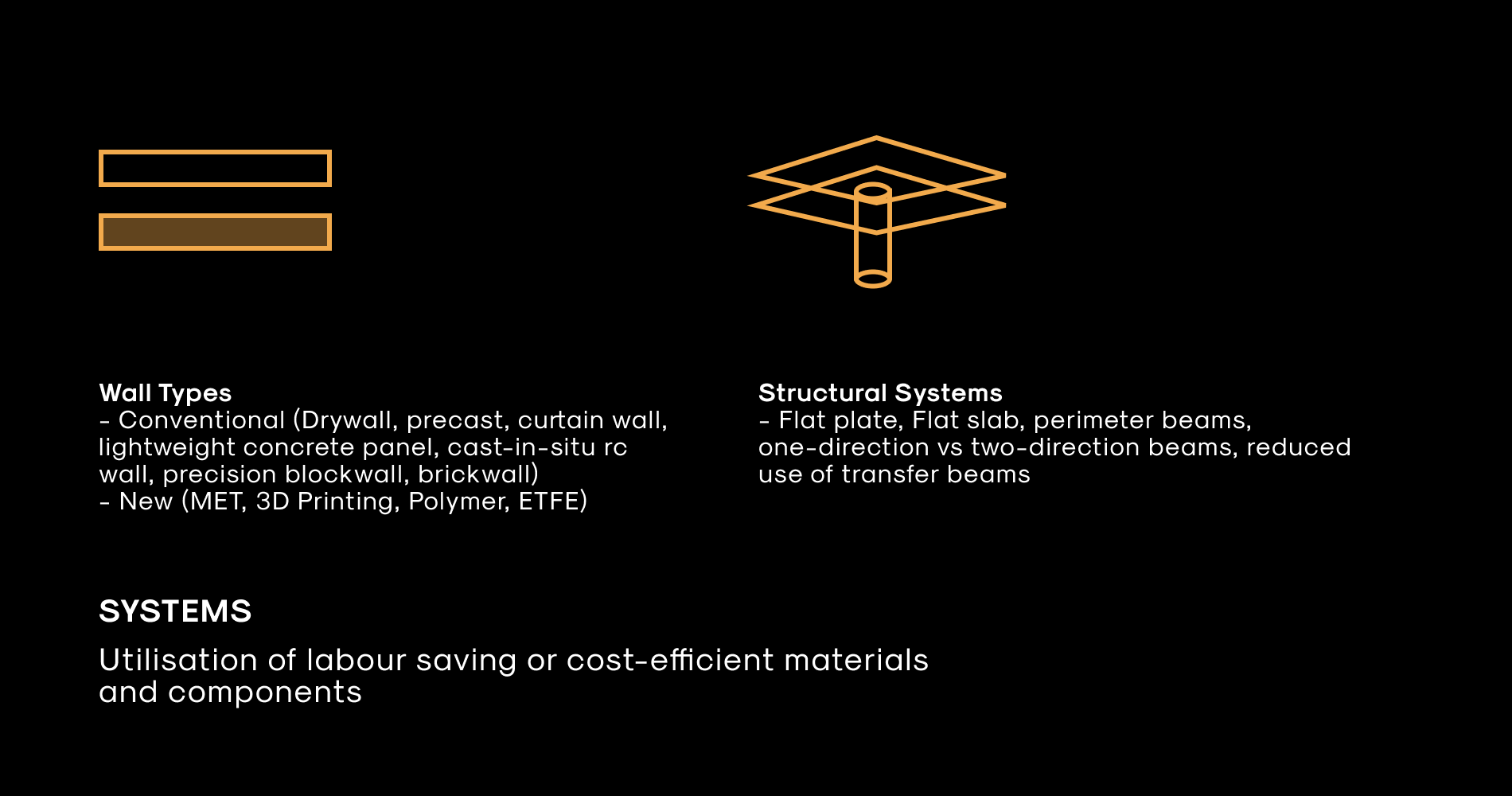
Here’s a pro tip, you should use a mix of high labour saving materials/systems as well as conventional materials.
This is because most ‘buildable’ material or systems are often times expensive - which might be a deterrent to use them. After all, it is the client who will be paying.
As material science progress, we will see new building process and materials being tested. These new materials will take over some of the current “expensive” materials that are highly labour/time/cost saving. Be assured that eventually, the industry will move more into buildable design.
How to Calculate Buildable Score
Inputs
- Wall length for each type
- Floor area/ Roof area for each type
- Percentage of repetition of grids, floor-to-floor height
- Number of types and dimensions of doors/windows/steps.
- Implementation of recommended building materials and/or systems (eg. Precast walls, pre-assembled staircases, prefab components)
Output
Points allocated to each of the above inputs and the sum of all of the components will give a final numeric score.
The minimum points required depends on GFA and occupancy type, and are checked by building authority.
Pro Tips
1) It's a Numbers Game
The implementation of productive building materials and systems are encouraged but not required excessively. Most developers are only eager to comply with minimum building regulations. So it is good to communicate and establish an understanding with them.
2) Unitise Systems
Integrating facade and wall systems into a modular solution results in a reduced wall length and thus a more optimised point allocation.
3) Do not limit your creativity
Lastly, while the idea is for architects to consider and use industry-wide design practices, it is also not advisable to be limited by these fixed dimensions if there is a strong reason to.
Resources
BCA (Singapore Building & Construction Authority)